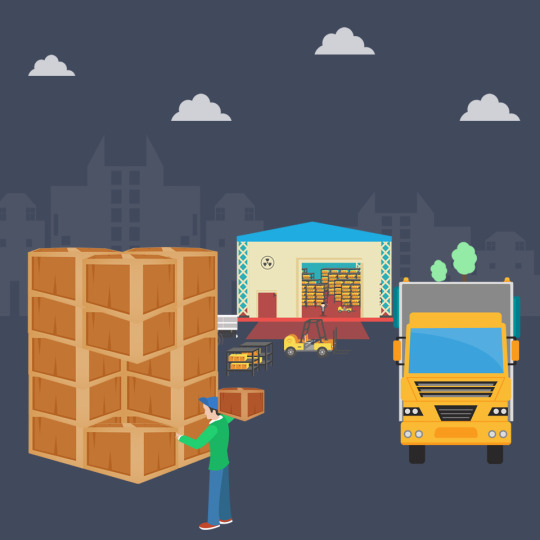
With the increase in growth of businesses, it is exceedingly challenging to manage orders. Here are a few tips to efficiently run your supply chain without being overwhelmed:
1. Accurate Demand Sensing and
Shaping
The first thing you get sorted in order
to establish successful order fulfilment is to have a good demand
management system. An advanced demand management aids in improving a
business’ ability to manage demand volatility, improve
demand-planning processes, and realize higher forecast accuracy. What
matters here are demand sensing and demand shaping. With customers
using various purchase channels, sometimes it becomes difficult to
capture purchase data. So, there are applications such as demand
signal repositories that allow companies to capture real time
multi-channel demand signals and analyze, through “slice and dice”
capabilities, the demand information to reveal patterns. This is
combined with demand history to provide insights for a more accurate
demand forecast. Other technological aids like trade promotions
optimization work together with demand sensing. These tools create
incentives to stimulate demand or optimize product promotions to
maximize growth and profitability.
These advanced demand management
capabilities can give accurate ideas on demands on a dynamic basis.
2. Global Order Promising
GOP enables organizations to make quick
delivery promises that customers can rely on. It allows organizations
to address customer related issues from basic “available to
promise” to “capable to promise” to “profitable to promise.”
GOP aligns real-time data-driven processes with manufacturers,
suppliers and logistics constraints so that organizations can have
more responsive, reliable, and profitable promising processes that
improve customer service levels and increases fill rates. Similarly,
retailers can use GOP to balance planning and execution when those
cycles are out of synch. Retailers with GOP now have complete
visibility into the supply chain and can take customer orders taking
into consideration the total order fulfilment cost.
3. Global Distributed Order
Orchestration and Fulfilment
The Distributed Order Orchestration
system enables organizations to apply enterprise-wide rules and
processes, and identify and rectify problems before they become an
issue for customers. Business managers have complete control over
order management processes and because of this, they are able to
monitor order progress, review issues, resolve problems, and modify
fulfilment processes as the business evolves. They can see real
margins during promising, fulfilment, and particularly expediting
activities and this improves their decision making.
These 3 factors can help an
organization revamp their order fulfilment systems and have a firm
grip on end to end logistics. The systems and tools drive
profitability and make sure that costs are optimised wherever there
is scope for cost optimization.